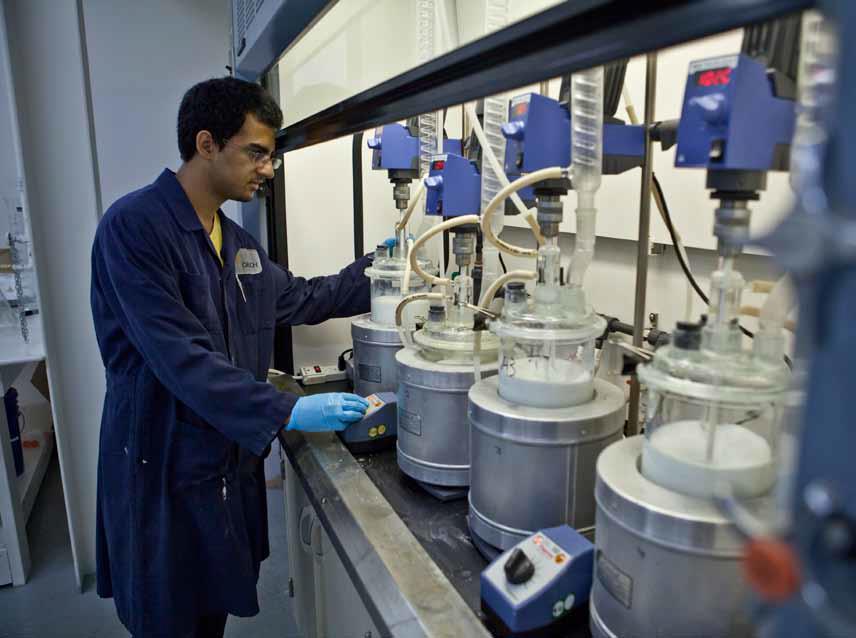
Canadian junior exploration company Argex Mining Inc. has been collaborating with global specialist chemicals company PPG Industries on a project that could revolutionise pigment supply in the paint industry. President and CEO Roy Bonnell talks to Gay Sutton about producing paint quality titanium dioxide pigment grade directly from run-of-mine ore.
For Montreal-based Argex Mining, the past year has been one of change. Now the company is poised to complete its transformation from a junior exploration company to a manufacturer of high grade titanium dioxide (TiO2) for the paint industry, using raw materials directly from the mine. And all of this is set against a back drop of rising market prices. At the end of 2010, TiO2 sold at around $2,500 a tonne. Prices currently stand at around $5,000, and are predicted to rise to $6,200 by 2015.
Argex has a portfolio of titanium bearing properties in Quebec. The first of these is La Blache, which was acquired in 2009 along with an iron bearing property Mouchalagane, and lies some 120 km northwest of the deepwater port of Baie-Comeau on the north shore of the St Lawrence River. An aggressive exploration programme on two of the titanium lenses was quickly launched in 2010 and confirmed an NI 43-101 compliant mineral resources estimate of 30.8 million tonnes of ore containing 18.78 percent TiO2 as well as 63.29 percent iron oxide and 0.45 percent vanadium pentoxide. The property portfolio was expanded in March this year with the acquisition of Lac Brule, also near Baie-Comeau, and known to contain TiO2 graded at around34 percent, although these have yet to be confirmed to NI 43-101 standards.
Interestingly, it was the market conditions during 2009 that led Argex directors to break away from the normal exploration company format, and to develop a strategy that would ultimately transform it both operationally and financially. “At that time, iron ore prices were horrific,” explained president and CEO Roy Bonnell, “and we came to the conclusion that if we could find an innovative new way to separate the iron from the titanium cost effectively, then we had a viable project at La Blache. So we started looking for the technology.”
The hunt for a new technology eventually took Argex toProcess Research ORTECH (PRO), a Canadian company that incubates and commercialises innovative technologies for process industries. PRO had already completed some preliminary work exploring the suitability of solvent extraction for processing titanium. Working with metallurgists at PRO and experts from PPG Industries, Argex invested heavily in developing the technology and ensuring it would be able to produce 99.8 percent pure pigment grade TiO2 directly from the mineral ore.
“We believe this is going to be a game changer,” Bonnell said. “The paint industry currently comprises miners, feed stock producers, upgraders and finally the paint companies. Right now, we’re seeing consolidation as companies acquire others in the supply chain to achieve vertical integration. Our technology enables us to capture that entire supply chain in one process.”
As part of the strategy to ensure the TiO2 produced by the new process would meet the exacting requirements of the paint and coatings industry, Argex approached key players in the industry, and began to develop a strong collaborative relationship with the global paints and coating company, PPG Industries.
By using solvent extraction rather than the sulphate or chloride processes currently in use, Argex will be able to avoid the environmental issues commonly associated with titanium extraction, and will also be able to remove contaminants. “The traditional TiO2 extraction processes are very limited in the type of deposits they can treat economically, as they are unable to remove many other elements and contaminants,” Bonnell said. “We will be able to remove them simply by adding another circuit to the process. So we should be able to produce high quality pigment grade TiO2 even from what is commonly called dirty ilmenite.”
Currently Argex has been trialling the process at a pilot plant in Mississauga just outside Toronto, not only testing the La Blache and Lac Brule ores, but also those from other sources. “It’s a very flexible technology,” Bonnell asserted. “We’ve successfully run ore through the plant from six or seven different ore bodies, and this raises a whole new set of prospects for us. If we are able to process high grade ores that other companies can’t treat because they’re unable to remove the contaminants, then we can decouple the plant from our own mines and access some very low cost sources of raw material. And this then becomes very exciting for the paint industry, as demand is increasing globally, while the supply of raw materials is a major bottleneck.”
The next step is to complete a feasibility study for the first $100 million industrial scale plant and then move on to financing and construction. And if all goes according to plan the first TiO2 plant is likely to be commissioned by mid-2014.
The introduction of new technology always presents risks. However, solvent extraction is widely used in the production of uranium, copper and nickel, and this works in Argex’s favour. While the new process is innovative in its use of the technology, it utilises standard equipment that is readily available and has been developed, tested and upscaled to industrial production in many applications worldwide. Meanwhile, the all-important patents for the process are held by Canada Titanium Ltd (CTL) which has been spun out of PRO, and the controlling interest has subsequently been acquired by Argex.
The CTL process also has a number of key advantages over the current processing methods: it has a very low environmental impact, operates at atmospheric pressure, does not require high temperatures and produces inert tailing that can then be used by the construction industry for raw material. “The comparative risk-profile for scale up with this technology is therefore very low,” said Bonnell.
“So I would say the last 10 months have been a real transition for us. We’ve taken Argex from being an exploration company to what is looking more like a speciality chemical company with a secure supply of raw materials,” he continued. The process of exploration is, by definition, taking a risk – drilling a hole and hoping it will reveal mineral resource. By contrast, a production company requires a solid financial foundation and business plan that minimises risk. “It’s a completely different mentality, and bridging that gap is what the past 10 months have been about.”
DOWNLOAD
ArgexMining-AM-May12-Bro-s.pdf